Reflection, glare, and… moths?
image via Wikipedia.
No, you don’t need to check the URL. You haven’t somehow been sent to an insect collecting site. This is still the good ol’ Android Authority you know and love, and I’m still here to tell you about some new developments in display technology. Stick around, we’ll get to the moths in a bit.
One of the most serious problems facing display designers — and one of the most difficult to deal with, especially in mobile devices — glare and reflections on the surface of a display. We like nice, polished screens. A glossy surface makes for a sharp, clear image. That same high-gloss finish makes for a pretty good mirror under certain lighting conditions as well. Seeing yourself in your phone screen (especially in the dark areas of an image) is distracting. Seeing the reflection of bright light sources can be downright uncomfortable, and often makes the screen completely unreadable.
Display makers have been trying to combat reflections and glare ever since the CRT was first introduced, to varying degrees of success. The simplest, cheapest measure taken is unfortunately one of the least effective: you can just rough up the surface of the glass (or whatever the front surface of your display is made of), giving it a matte finish. This was pretty common in the CRT monitors of the ’70s and ’80s, but fell out of favor — for a glaringly (pardon the pun) obvious reason. A rougher surface makes reflections a lot less distinct (rather than looking like a mirror, light reflected by the screen surface just becomes a hazy glow), but still reflects just as much light.
A rougher surface makes reflections a lot less distinct, but still reflects just as much light.
For this little bit of questionable benefit, you get the added bonus of having your displayed images look hazy and out of focus, too! In the ’90s, the highly-polished CRT came back into fashion (the so-called “glare screens”), and we all just lived with having mirror-finish displays as the cost of wanting crisp, sharp images.
Oddly enough, when LCDs started displacing CRTs in PC monitors, they had matte-finish screens just like the older CRTs, and this was actually touted as one of their advantages over CRT monitors! Again, people quickly tired of trading perceived display sharpness for a finish which really just spread the glare out into a haze instead of actually reducing it.
Today, especially in our mobile devices, polished screen surfaces are the norm. But for those who want a matte surface, “anti-glare” matte finish “screen protector” films are widely available. All they really do is diffuse the glare, not reduce the amount of light being reflected. Who’d have thought.
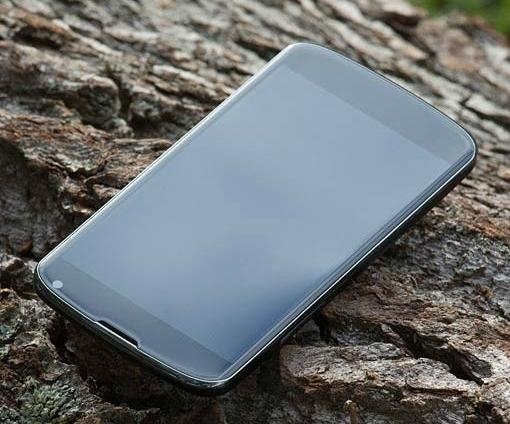
A matte finish screen protector. Such surfaces don’t really reduce glare — They just diffuse it. China-Direct-Buy.com.
There is (and has been for some time) a third option. There are true anti-glare surface treatments that actually reduce the amount light reflected from the glass. To understand how they work, we have to take a look at what causes glare in the first place, which is more complicated than you might at first imagine.
There are true anti-glare surface treatments that actually reduce the percentage of light reflected from the glass.
Glass is, of course, a transparent substance. Light passes right through it, apparently like it isn’t there at all, as anyone who’s walked into a closed glass door can attest. Where light is completely reflected by an opaque material, it passes through a transparent one — except when it doesn’t. If you’re shining a light on a highly polished glass surface, about 96 percent of the light will go straight through, and four percent will be reflected.
As an aside, this is actually a bit of a mystery, if we accept quantum mechanics and believe light and other electromagnetic waves are really streams of particles we call photons. All photons have to be identical. But if this is so, how do 96 photons out of every 100 “know” they’re supposed to go through the surface, while the other 4 “know” they’re supposed to be reflected? This question still has not been satisfactorily answered.
Leaving that problem for the theoretical physicists, something very interesting happens when you add a second reflecting surface below the first. Given what we just said about 4 percent of the light reflecting back and 96 percent getting through when it strikes such a surface, we might expect that to happen again with a second surface, resulting in a little under 8 percent reflected back at the viewer (the original 4 percent, plus another 4 percent of the 96 percent that went through the first surface). When we actually try a setup like this, something odd happens; the total light reflected back to an observer can range from zero to 16 percent! It turns out this total reflection percentage depends on how thick that layer between the first and second surfaces is.
Don’t miss: Are micro-LEDs the new OLEDs?
A very, very thin surface results in a total reflection of zero, and as you increase the thickness the reflection climbs to a peak of 16 percent and then goes back down to zero! This cycle repeats, over and over again, as the thickness varies. If you look a little further into this, it turns out the cycle is related to the wavelength of the light in question, and at least this part of the phenomenon is explained fairly easily if we stick to the wave model of light. Without explaining just why a certain percentage of the light is reflected in the first place, we can at least say a reflection that occurs a quarter-wavelength “below” the first one should cause an overall reduction in the total amount of reflected light. This is because the total path length from the first surface to the second and back again is one-half wavelength — so the second-surface reflection comes back 180 degrees out of phase with the first and cancels it out.

Entekno Materials Quarter-wave AR coatings cancel reflections via destructive interference
This leads us to one of the most effective anti-glare treatments for display screens to date, the quarter-wave anti-reflective (or “AR”) coating. A thin layer of material, chosen for its refractive index and durability, is applied (usually via vacuum deposition) to a glass surface. The process is controlled so the thickness of this layer winds up being about a quarter of the wavelength of light in this medium, producing the effect just described.
Glass treated in this manner can have a total reflection of one percent or less, a significant improvement from the untreated case.
Of course, there are disadvantages to this as well. Besides the added cost of the treatment, the coating can really only be a quarter-wavelength thick at one specific wavelength, which causes some color effects. The thickness is generally adjusted to be a quarter wave around the center of the visible range, which corresponds to the greens on the visible spectrum. This means the anti-reflective effect is strongest there, and less so in the reds and blues. It also gives a purplish hue to the reflections that remain. Screens treated in this manner also tend to show fingerprints more, as the oil in them interferes with the AR effect.
A new approach to controlling reflections has started to come to market based on moth's eyes.
More recently, a new approach to controlling reflections has started to come to the market. This is where we get back to the insect that started this article. It’s been known for quite some time that moth’s eyes reflect very little light; it’s something they’ve evolved to avoid predators during their mostly-nighttime lives. Investigating how this is achieved shows that the moth’s eyes are covered with millions of microscopic protrusions. Light striking this surface is not reflected back, but rather directed mostly “downward,” further into the protrusions where it is then absorbed.

Artificial moth’s eye structures created in silicon. Via Brookhaven National Lab.
Today, scientists have discovered ways of producing similar structures on the surface of glass. We covered one back in one back in November 2017. If suitable production methods can be developed, and such a surface can be made durable enough for the rigors of everyday use, this type of anti-glare treatment could result in screens that reflect virtually no light, producing sharp, clear images with very high contrast. It’s even possible such a surface could be made in a form suitable for flexible screens. The “moth’s-eye film” approach to glare reduction is still a long way from commercial implementation, though.
When it’s ready, we’ll have virtually reflection-free screens with unmatched contrast and sharpness — and a moth to thank for it all.
Comments
Post a Comment